If you havent already clip the flange washer onto body II, Re-align Clutch B frictions and install body II assembly into Clutch B ensuring all frictions engaged; lift and drop Body II slightly, a metallic sound confirms fully seated, a muffled sound its not fully seated. This took some patience to get seated corrrectly
To verify its seated correctly check the dimension from the top face of body II to the ATF pump ledge in the gearbox, it should be approx 12mm. If its much less its not seated correctly.
If you cant get it to seat correctly (it wont go down) and you are sure its not being held on a friction, and you have changed the bushes; then check the installed depth of the new bushes is correct, ie one of the shafts is not bottoming onto a bush.
Install the 4 new rubber Tubes into the ports interfacing Clutch C/D to the valve body; I measured these for comparison to the old ones, which we review at the end
Without fitting the last selective shim washer (that sets the input shaft axial play) I did a trial fit of the pump housing and assembly to make sure it went down ok just fitting 4 screws spaced out 90 degrees each using the old U-Sit washers. I then took a DTI measurement of the axial play at this stage to determine how much play the box has with no shim washer
Then I removed the oil pump housing again and fit the selective shim washer I had, which I measured as 3.2mm
Then I refit those 4 screws with the old U-Sit sealing washers again 90degrees apart and took another DTI measurement of the input shaft axial play
My measurement with no washer fitted was 2.08mm
My measurement with my 3.2mm selective shim washer was 0.462mm;
Clearly the washer is partially recessed and not fully accounting for the clearance from body II to the oil pump housing
Also since the specified allowable tolerance on the axial play is 0.2-0.4 (no more no less) -strictly speaking I need to order a 3.4mm shim washer.
Its about now Im thinking ok so its only 0.062mm...... and Ive been without my RS6 for a number of weeks.... So I went with it and accepted the slightly large tolerance. I wouldnt have accepted much more than this, and I wouldnt have accepted anything less than the 0.2 the other way.
So whip out the 4 old screws with their old U-Sit sealing washers and use the set that came in the overhaul kit
I should have mentioned all of this trial fitting and final fitting of the pump housing is with a NEW sealing O-Ring from the overhaul kit fitted and vaselined
Remember the tightening sequence 1 through 14, and torque these to 10Nm ( I do them in increments 2Nm, 5Nm, 10Nm)
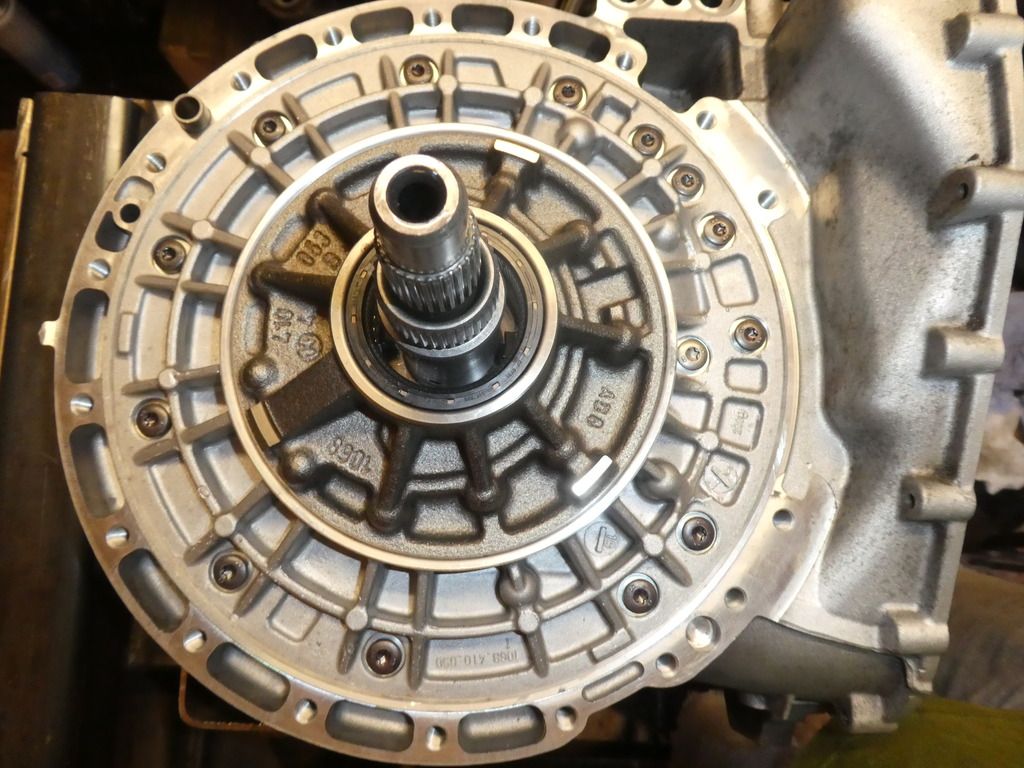
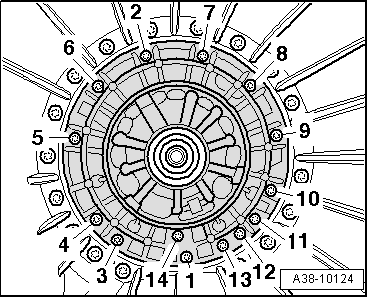