Over the last 6 months JBS Developments has been busy working on a new cast K03 manifold, and now that the new K03 is heading into the final stages of production we have moved onto the K04 turbo application.
From what JBS has learnt from the development of the K03, the design process for the new K04 OEM performance upgrade manifold became a lot simpler.
Casting the new manifold gives better quality mass production and for such a constraint bound design as the K04 manifold casting gives fewer constraints on the pipe bend radiuses, allowing the runner to flow freely.
The most obvious improvement over the standard cast manifold being the increase in bore (diameter) of the runners all the way into the collector.
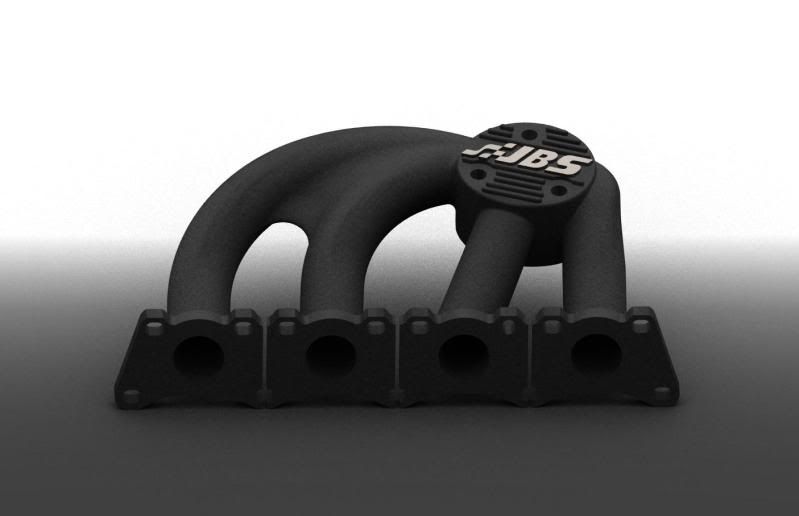
Like the new K03 design, the manifold has been designed in CAD to optimise the design, flow capabilities and to enable easier fitment. The CAD process allows the designers at JBS to manipulate the part quickly, while allowing information and measurements to be taken easily.


JBS K04 SPEC
The main work has taken place increasing the diameter of the runners all the way to the collector and the design of the collector to achieve best flow. The manifold has been designed to have maximum material around the bolt holes to prevent cracking, found on the OEM and competitors manifolds. The collectors design also separates the runners to reduce port sharing of combusted gasses, aiming them towards the turbine in the turbo.
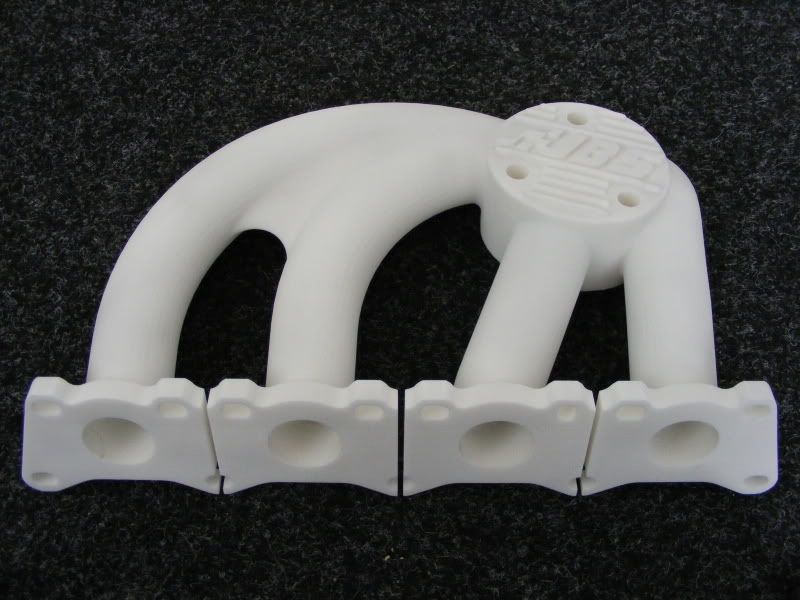


The box collector features cooling fins to minimise the effects of EGT’s on the manifold, preventing the manifold from warping and thermal fatigue.
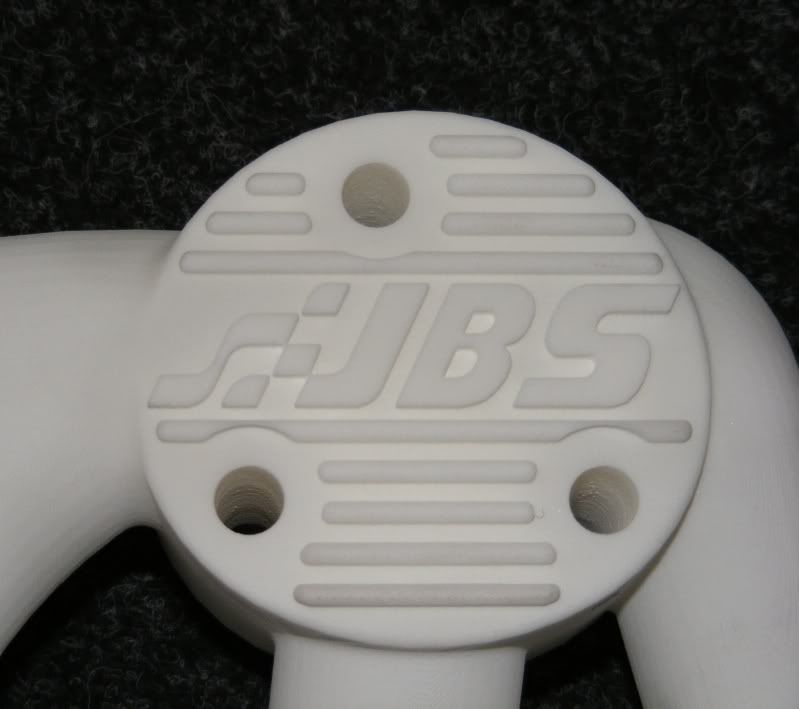
Fitment of the manifold was also a large consideration, the area around the head studs and nuts was maximised to enable fitment.
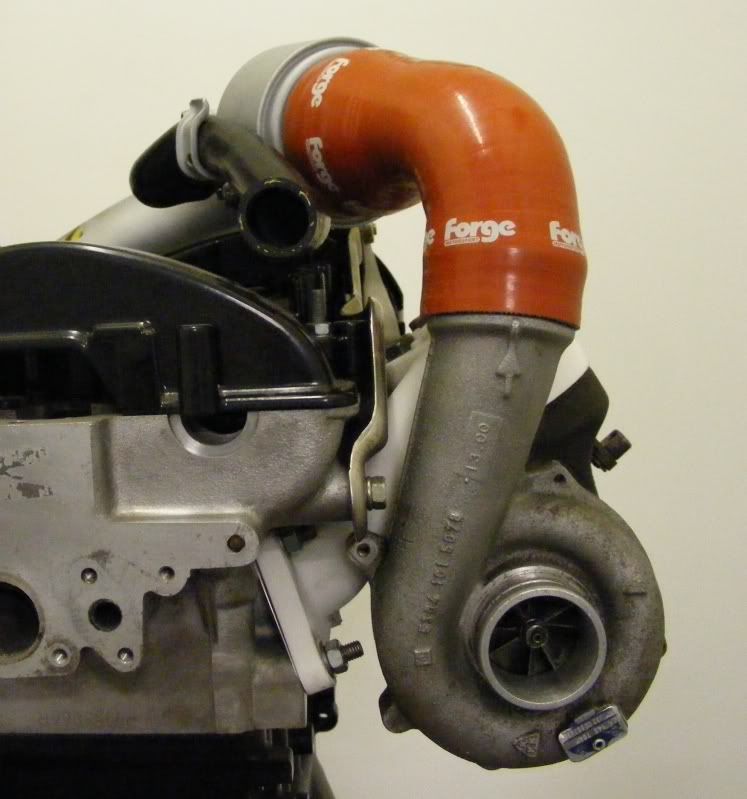
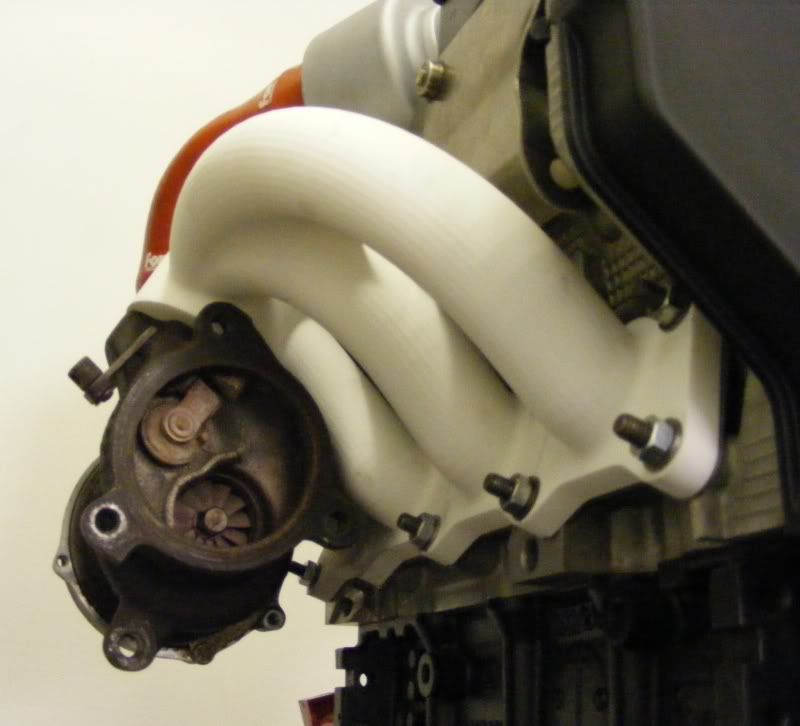

The cylinder head flange uses the same design as the K03 to allow greater thermal expansion and movement between the runners. As it was found that a too restrictive flange forced stresses back through the runners of the manifold which lead to crack propagation.
Once we were happy with our design it was sent off for rapid prototyping to give us a physical model to evaluate before any design finalisation can take place. The rapid prototype is a highly accurate model taken straight from the CAD data.
The RP (Rapid Prototyping) gives a huge advantage in being able to fit the part to an engine and turbo, to test and ensure that the product achieves its specification. We are also able to physically flow test our design and compare it to our CFD (computational fluid dynamics) data before being sent for casting.

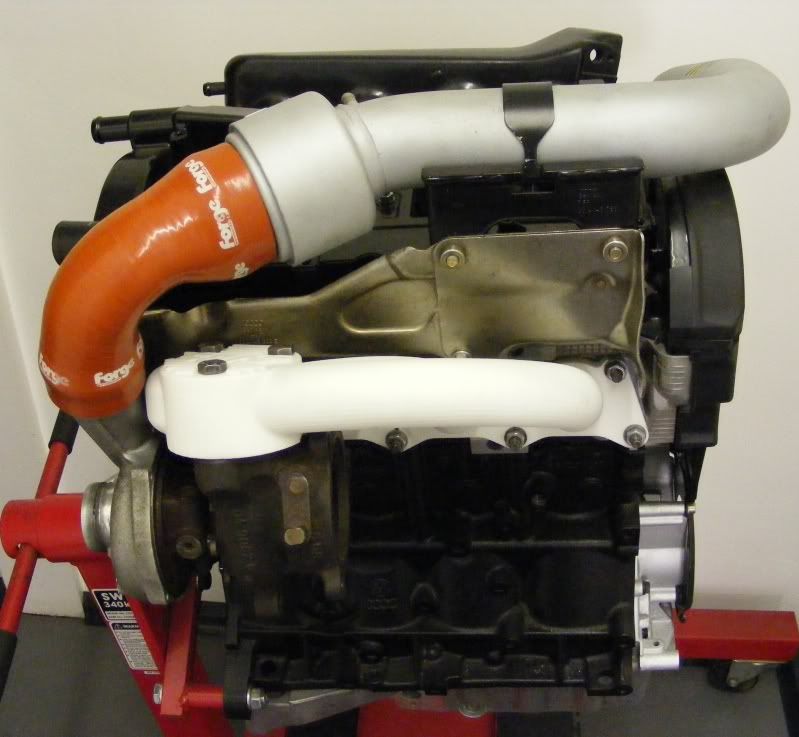
Recently there has been a lot of talk about performance manifolds cracking due to poor design, weak materials and the stress the manifolds are under due to high exhaust gas temperatures. JBS JBS Developments are confident in the design of the new manifolds due to the hours spent on CFD (computational fluid dynamics) analysis and prototyping.
So to ensure the manifolds don’t suffer from poor material choice and casting quality, JBS has chosen to cast its manifolds in a very high quality foundry which is used by many OEM turbo suppliers and OEM vehicle manufacturers such as BMW and GMC to ensure the castings are of the highest quality.
Also to reflect the high quality casting; JBS has spent a great deal of time researching the latest high temperature resistant cast irons. These cast irons have a high nickel content, having the following properties makes them ideal for our performance manifolds: resistance to corrosion, resistance to oxidisation and high temperatures (up to 1050 oC), resistance to wear and erosion.
This is to ensure a minimal amount of thermal expansion and an equal rate of thermal expansion to the turbo housing, this again minimises the potential for thermal fatigue (cracking). The bolts for the fitment of the turbo to the manifold shall be supplied as they are a specific size and material to prevent stretching which leads to blowing gaskets.
JBS Developments are now waiting for the pre-production sample to be delivered for a quality check and initial testing.
Once the first batch of manifolds are produced, they shall be thoroughly tested and dyno’d. At which time all power and flow figures will be released. Once all testing is completed and we are happy with the results we aim to release the manifolds at £470 including bolts and VAT.
We also have an IHI stage one/ Garrett GT28 cast manifold going into production and the K03 will be released soon. As well as having our new range of tubular equal length manifolds for IHI, T2, T3 and Twin Scroll on sale now.
JBS Developments